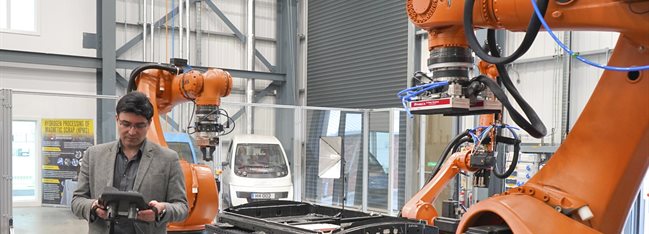
At the Birmingham Energy Innovation Centre (BEIC) based on the Tysley Energy Park (TEP) you will find the Extreme Robotics Lab's (ERL) full-scale industrial manipulators housed in an academic research environment which offers an ideal platform for industry-academia collaboration and innovation. The ERL's Sustainable Robotics Centre (SRC) has been designed by leading robotics and AI experts at University of Birmingham’s Extreme Robotics Lab, and developed with KUKA-UK, featuring a combination of large-scale KUKA heavy duty manipulators, advanced dexterous arms, actuated positioner systems, advanced tooling, and high-spec vision and sensor systems. The facility has been entirely created and supported by competitively won research grants, with funding from: UKRI-ISCF; EPSRC; Faraday Institution; Horizon Europe; and direct funding from industry.
Professor Rustam Stolkin
Chair of Robotics, University of Birmingham
“The NSRC is an industrial-scale research facility that serves as a vital bridge between academia and industry.”
A current focus is robotic disassembly of complex end-of-life products, such as the large Lithium Ion battery packs of Electric Vehicles. However, the facility includes a pair of large KUKA KR500 robot arms, identical to those being installed in UK nuclear sites for legacy waste handling in coming decades. Other ongoing work includes developing advanced motion-planning for long-reach many-joint manipulators for decommissioning at Fukushima Daiichi NPP and other nuclear sites. Our robots are also appropriate for developing and demonstrating a variety of manufacturing automation solutions at scale.
The SRC combines UoB-ERL’s internationally prominent expertise in advanced robotic manipulation combined with AI, computer vision and sensory-driven control, with a full-scale industrial robot demonstrator housed in a highly flexible research environment, where novel solutions can be rapidly developed for a wide range of industrial challenges.
These technologies are currently being utilized to automate disassembly processes for EV batteries, covering disassembly from pack to cell level. Furthermore, the SRC employs machine learning methods to estimate the state of health and remaining useful life of batteries, contributing to the efficient management of battery resources.
By collaborating with the SRC and its team of experts from the Extreme Robotics Lab (ERL), research organizations, universities, and industry stakeholders have the opportunity to engage in a variety of future-looking projects, and progress them through from lower Technology Readiness Levels (TRL) to higher TRLs. Such collaborations also provides access to the internationally leading experts and equipment of the ERL lab at UoB’s Edgbaston campus, one of UK’s largest, newest and best-equipped robotics R&D facilities. This combination enables researchers and industry professionals to conduct industrial-scale experiments while benefitting from cutting-edge resources.
EV battery disassembly at the ERL NSRC
Current ERL SRC projects include:
-
Horizon Europe: REBELION, 2023-2026 – Research and development of a highly automated and safe streamlined process for increased Lithium-ion battery repurposing and recycling
This is a €5.5 million EU project that aims to advance the technology of EV battery disassembly using advanced robotics and AI. The project aims to develop a generalizable automation techniques for the disassembly of different EV battery models by creating digital passports and adaptive task planners.
-
Faraday Institution: ReLiB, 2018-2024 – Reuse and Recycling of Lithium-ion Batteries
The overall aim of the ReLiB project is to understand the conditions required to ensure the sustainable management of lithium-ion batteries when they reach the end of their useful life in electric vehicles. The SRC is a pioneering national robotic center that benefits from the state-of-the-art scientific knowledge gained in academia regarding EV batteries.
-
UK Atomic Energy Authority: Advanced motion planning and control of long-reach high-degree-of-freedom robot arms, 2022-2024
This project is developing motion planning algorithms, with respect to scenes captured by 3D computer vision, to enable many-jointed, long-reach manipulators to safely negotiate complex, cluttered environments while avoiding collisions. Such manipulators are being developed for retrieving fuel debris from damaged reactors at the Fukushima Daiichi NPP accident site. Many-joint arms are also used for servicing and eventual decommissioning of the JET experimental fusion torus at UKAEA Culham, may be used in future fusion reactors such as ITER, and may also be needed for other decommissioning tasks at legacy nuclear sites such as Sellafield in the UK. Collision-free motion planning of many-jointed manipulators pose extremely challenging mathematical problems of searching for, and optimising, viable trajectories through high-dimensional joint spaces, e.g. a 13-dimensional search space for our experimental 13-joint 5-metres reach arm at SRC-BEIC.